Screen printing, a technique rooted in history yet vibrant in modern application, offers an unparalleled avenue for creating vivid, durable designs on a multitude of surfaces. This blog delves into the complexities of screen printing, spotlighting the nuanced steps and technical considerations essential for producing premium printed materials. Furthermore, we'll explore the significant advantages of utilizing 100% water-based inks, underlining their role in enhancing color vibrancy, durability, and sustainability in screen-printed products.
The Intricacies of Screen Printing
The Genesis of a Design
The journey begins with a transparent acetate film, which acts as a blueprint for the forthcoming design. This film is pivotal in demarcating the inked and non-inked regions on the screen.
Screen Preparation and Emulsion
A distinct screen is allocated for each color in the design, with mesh counts tailored to the intricacy of the design. The screen is coated with a light-reactive emulsion, setting the stage for the creation of the stencil.
The Magic of Light Exposure
Positioning the acetate film atop the emulsion-coated screen, the setup is then exposed to bright light. This exposure hardens the emulsion, except where shielded by the design, crafting a precise stencil on the screen.
The Emergence of the Design
Post-exposure, the screen is bathed in water, washing away unhardened emulsion and unveiling the design imprinted on the mesh.
The Act of Printing
The screen, now a bearer of the design, is secured over the printing board. The material awaiting the design is placed beneath, ready to receive the ink forced through the mesh by a squeegee, thus breathing life into the design.
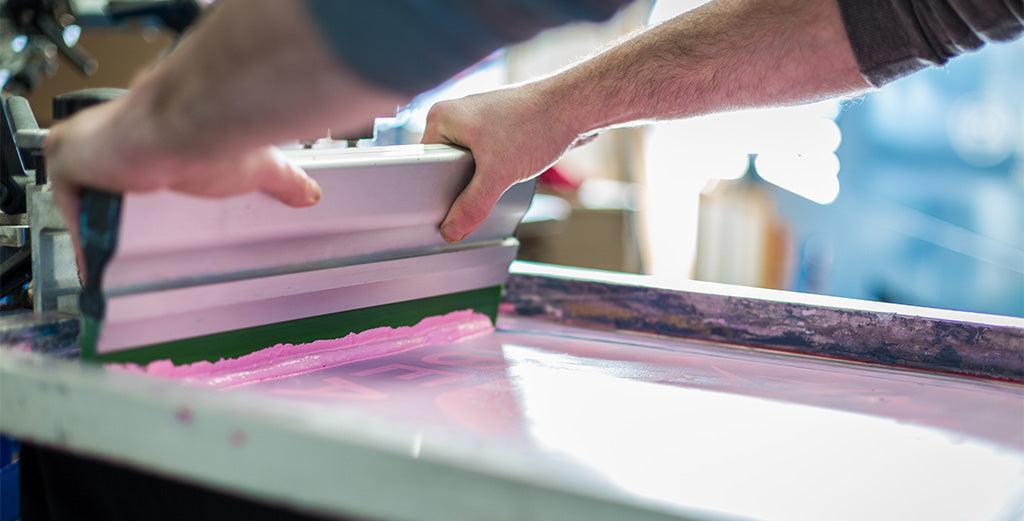
Overcoming Material Complexities
Screen printing on materials like high-polyester fabrics necessitates meticulous adjustments to prevent slipping and blurred edges, ensuring the integrity of the printed design.
The Finishing Touches
Flash Curing
A prelude to the final cure, flash curing momentarily heats the ink, priming it for subsequent layers and preventing color bleed.
Final Curing with a Heat Tunnel
The culmination of the process sees the ink undergoing a thorough cure in a heat tunnel, solidifying the design's resilience and vibrancy.
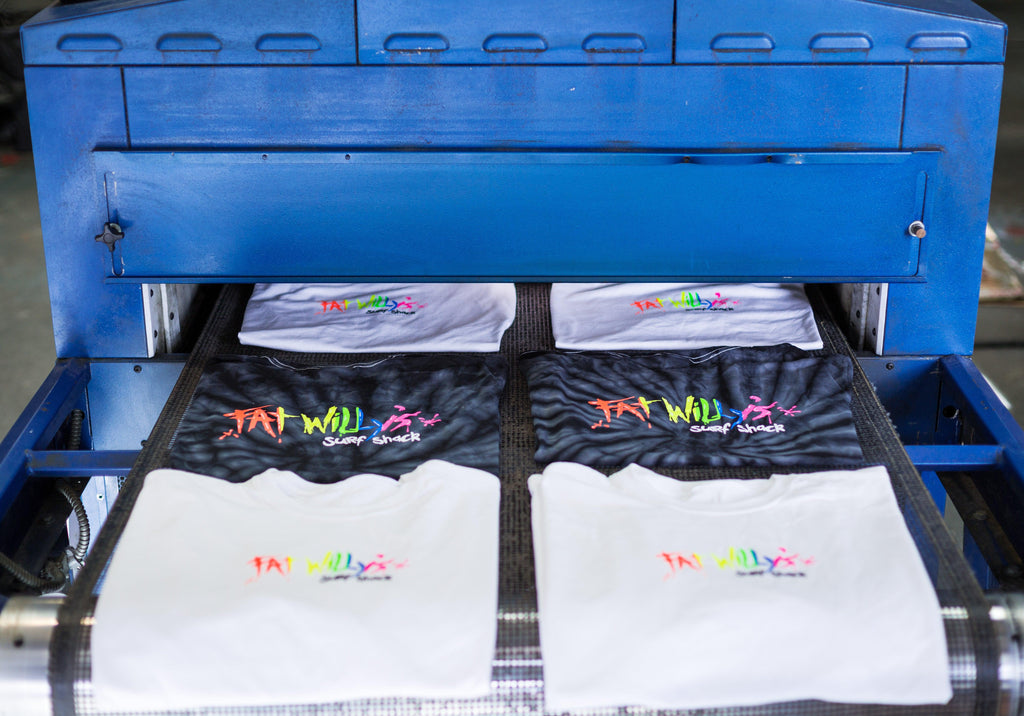
Elevating Screen Printing with Water-Based Inks
Our commitment transcends traditional screen printing techniques; we champion the use of 100% water-based inks. This choice is deliberate, reflecting our dedication to delivering not just visually appealing and long-lasting prints, but also products that resonate with eco-conscious values and brand integrity.
The Pinnacle of Print Quality
Water-based inks infuse the fabric, ensuring that each print is a testament to durability and color richness, essential for high-quality brand merchandise.
Fostering Brand Trust
By prioritizing superior print quality, we help brands cultivate trust and loyalty among customers, affirming the brand's dedication to excellence and reliability.
A Nod to Sustainability
Choosing water-based inks aligns with our environmental ethos, offering a safer, more sustainable printing solution that appeals to the eco-aware consumer.
A Harmonious Blend of Quality and Responsibility
Our approach to screen printing marries quality with sustainability, offering brands a competitive edge through products that not only stand out for their excellence but also their environmental stewardship.
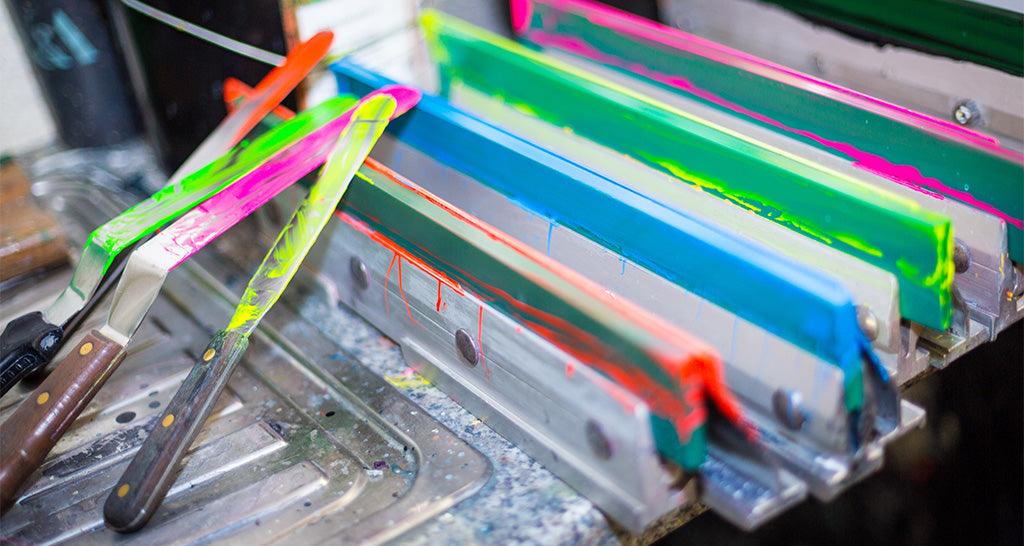
Conclusion
Screen printing is more than a printing technique; it's a craft that balances artistry with technical precision, and when augmented with the use of water-based inks, it transcends to embody sustainability and quality. This blend of tradition, innovation, and responsibility makes screen printing an invaluable asset for brands aiming to leave a lasting impression on their audience while upholding values of environmental care and product excellence.